Alcast Company Fundamentals Explained
Table of ContentsSome Ideas on Alcast Company You Need To KnowThe Buzz on Alcast CompanyThe Only Guide for Alcast CompanyA Biased View of Alcast CompanyThe 5-Minute Rule for Alcast CompanyThings about Alcast Company
The subtle difference exists in the chemical material. Chemical Contrast of Cast Light weight aluminum Alloys Silicon advertises castability by minimizing the alloy's melting temperature and enhancing fluidity throughout casting. It plays a vital duty in allowing complex mold and mildews to be filled up precisely. Additionally, silicon contributes to the alloy's strength and use resistance, making it beneficial in applications where resilience is critical, such as auto components and engine parts.It also enhances the machinability of the alloy, making it easier to refine right into ended up items. This way, iron contributes to the total workability of light weight aluminum alloys. Copper enhances electric conductivity, making it helpful in electrical applications. It additionally improves corrosion resistance and contributes to the alloy's total toughness.
Manganese adds to the toughness of aluminum alloys and improves workability (Casting Foundry). It is typically made use of in functioned aluminum products like sheets, extrusions, and accounts. The visibility of manganese help in the alloy's formability and resistance to breaking during fabrication processes. Magnesium is a lightweight component that supplies stamina and influence resistance to aluminum alloys.
See This Report on Alcast Company
Zinc enhances the castability of aluminum alloys and helps manage the solidification procedure during spreading. It enhances the alloy's stamina and hardness.
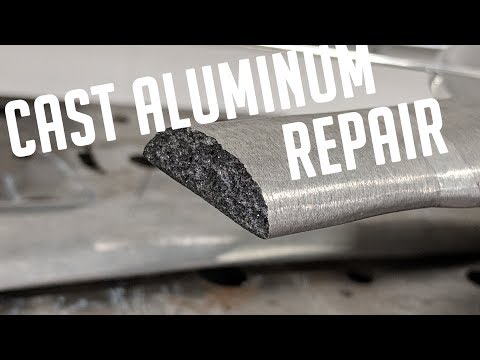
The main thermal conductivity, tensile strength, return strength, and prolongation vary. Among the above alloys, A356 has the greatest thermal conductivity, and A380 and ADC12 have the most affordable.
Facts About Alcast Company Uncovered

Its unique residential or commercial properties make A360 a beneficial option for accuracy spreading in these markets, enhancing item durability and high quality. aluminum casting manufacturer. Light weight aluminum alloy 380, or A380, is a commonly used spreading alloy with several distinctive attributes.
In accuracy casting, aluminum 413 shines in the Customer Electronics and Power Tools sectors. This alloy's remarkable rust resistance makes it an exceptional option for exterior applications, making sure resilient, resilient products in the pointed out sectors.
How Alcast Company can Save You Time, Stress, and Money.
As soon as you have determined that the light weight aluminum pass away casting procedure appropriates for your job, an essential next step is choosing one of the most appropriate alloy. The aluminum alloy you select will substantially affect both the spreading procedure and the properties of the end product. Due to this, you must make your choice thoroughly and take an enlightened approach.
Identifying the most appropriate light weight aluminum alloy for your application will certainly suggest considering a vast range of features. The very first category addresses alloy characteristics that impact the production process.
How Alcast Company can Save You Time, Stress, and Money.
The alloy you pick for die spreading straight impacts numerous facets of the casting procedure, like how simple the alloy is to work with and if it is vulnerable to this post casting flaws. Warm cracking, also referred to as solidification splitting, is a common die casting flaw for aluminum alloys that can result in internal or surface-level rips or splits.
Particular aluminum alloys are a lot more susceptible to warm breaking than others, and your option ought to consider this. It can damage both the actors and the die, so you must look for alloys with high anti-soldering homes.
Rust resistance, which is already a noteworthy characteristic of aluminum, can differ considerably from alloy to alloy and is a necessary particular to think about depending upon the environmental conditions your item will certainly be exposed to (Aluminum Casting). Use resistance is an additional home commonly looked for in aluminum products and can differentiate some alloys